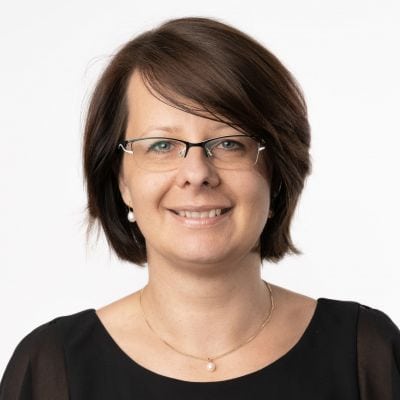
Maßgeschneiderte Wasserstoffspeicherung in Autos
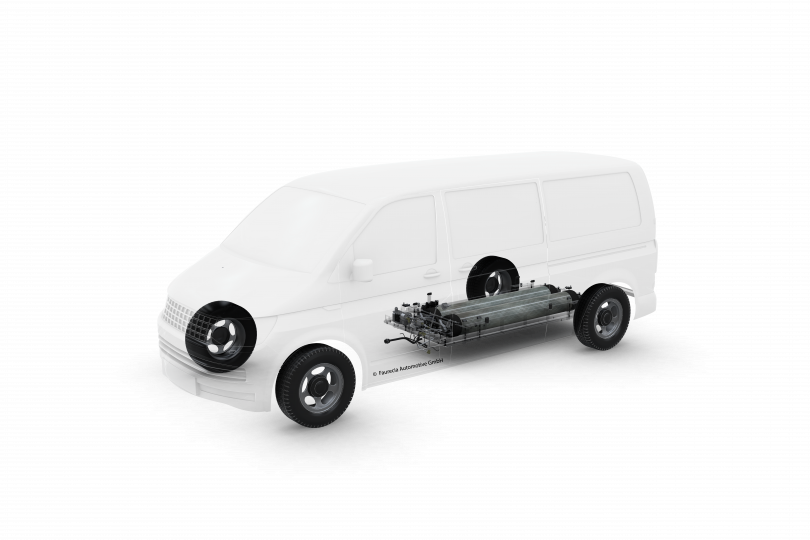
Als klimaneutraler Energieträger bietet grüner Wasserstoff großes Potenzial – auch als Kraftstoff für Autos. Momentan sind batterieelektrische Fahrzeuge die vorherrschende umweltfreundliche Alternative zu Verbrennern. Brennstoffzellenfahrzeuge stellen für Autofahrer jedoch eine vielversprechende Alternative dar. Gerade für lange Fahrstrecken, bieten sie Vorteile wie kurze Betankungszeiten und geringe saisonale Reichweiten-Reduzierung. Ein großer Nachteil von Wasserstoffautos ist der hohe Preis für Endkunden, der auf das geringere Produktionsvolumen zurückzuführen ist. Eine vielversprechende Möglichkeit, die Kosten durch Skaleneffekte zu senken, ist die Verwendung gemeinsamer Fahrzeugarchitekturen für Batterie- und Brennstoffzellenfahrzeuge. In diesem Fall steht ein flacher Bauraum (Raum, der für den Einbau bestimmter Dinge zur Verfügung steht) im Fahrzeugunterboden für das Wasserstoffspeichersystem zur Verfügung. Derzeit wird Wasserstoff in PKWs typischerweise gasförmig bei 70 MPa in zylindrischen Faserverbund-Druckbehältern gespeichert. Für den flachen Bauraum im Fahrzeugunterboden sind zylindrische Druckbehälter allerdings nur bedingt geeignet. An den Bauraum angepasste quaderförmige Behälter bieten großes Potenzial zur optimalen Ausnutzung des Volumens und damit zur Erzielung größerer Reichweiten.
Bisher finden an den Bauraum angepasste Wasserstoffspeicher noch keine praktische Anwendung in Fahrzeugen. Während die Behälterwand in zylindrischen und kugelförmigen Tanks maßgeblich auf Zug belastet ist, treten in Behältern mit abweichenden Geometrien unter Innendruck hohe Biegekräfte auf. Dadurch ist es bei solchen Tanks zielführend, Verstärkungsstrukturen im Tankinneren einzubauen. Vor allem für leichte Faserverbundtanks resultiert das in fertigungstechnischen Herausforderungen. Um diese Herausforderungen zu adressieren, müssen neue Ansätze unter Einbeziehung etablierter, serientauglicher Fertigungsprozesse, entwickelt werden. Deshalb wird im Rahmen des COMET-Moduls „Polymers4Hyd-rogen“ an der Technischen Universität München an einem neuen Fertigungs-Konzept für bauraumangepasste Faserverbundtanks geforscht.
Neuer Fertigungs-Prozess
Der innovative Prozess besteht aus vier grundlegenden Schritten und bietet die Möglichkeit einen Faserverbundtank mit integrierten Zugstreben unter Nutzung des etablierten Wickelverfahrens zu fertigen. Die Anbindung der Streben an die Tankwand ist entscheidend, da hier maßgeblich die dem Innendruck entgegenwirkenden Kräfte eingeleitet werden. Da bei dem entwickelten Konzept die umgeformten Enden der Streben in verschiedenen Lagen des CFK-Laminats verankert sind, wird eine fasergerechte Lasteinleitung erzielt.
Wirkungen und Effekte
Das im COMET-Modul „Polymers4Hydrogen“ entwickelte Fertigungs-Konzept ermöglicht die Herstellung von leichten Faserverbundtanks mit bauraumangepasster Geometrie. Das bietet großes Potenzial für die Nutzung gemeinsamer Fahrzeugarchitekturen bei Batterie- und Brennstoffzellenfahrzeugen, was durch Skaleneffekte zu einer Kostenreduktion des Gesamtsystems führt.