ATM Recyclingsystems: „Restlverwertung rechnet sich.“
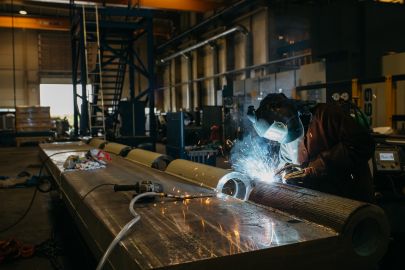
ATM investiert sehr viel Zeit und Geld in die Aus- und Weiterbildung der Angestellten, denn kompetente MitarbeiterInnen sind ein Erfolgsfaktor: CTO Andreas Anbauer berichtet voller Stolz von zwei ATM-Lehrlingen, die die Lehrabschlussprüfung kürzlich mit Auszeichnung bestanden. Zuletzt absolvierten die beiden neben Berufsschule und Betrieb 480 zusätzliche Einheiten – das entspricht 80 Schultagen – im Schulungszentrum Fohnsdorf, um ihre Skills im Maschinen- und Metallbau zu verfeinern. Die SFG übernahm rund ein Drittel der Kosten.
„Unser Produktportfolio wird immer größer. Das bedeutet, dass unsere Leute immer mehr können müssen.“CTO Andreas Anbauer
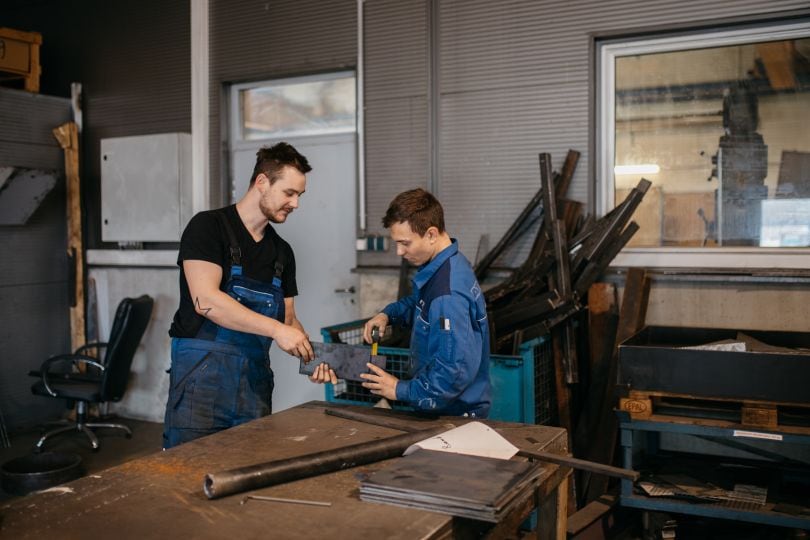
Restlverwertung bei Volvo
ATM baut Anlagen für die Prozess- und Automobilindustrie. So schneidet beispielsweise Volvo Karosserien aus Metallplatten und presst im Anschluss die Reste mit einer Maschine von ATM zu Paketen, die wiederum eingeschmolzen und zu neuen Metallplatten verarbeitet werden. Ganz so, als würde man die Reste der ausgestochenen Weihnachtskekse wieder zu einem Teig kneten und die nächste Partie ausstechen. Eine besondere Herausforderung sind die gewaltigen Dimensionen der Maschinen: „Eine ‚kleine‘ Anlage braucht ungefähr so viel Strom wie ein ganzer Betrieb mit 4 Bearbeitungsmaschinen insgesamt“, verdeutlicht Anbauer. ATM exportiert nach Europa, Amerika und Russland.
Pioniere der Nachhaltigkeit
In puncto Nachhaltigkeit war ATM seiner Zeit um Jahrzehnte voraus: Die erste Schrottschere entwickelte das Unternehmen bereits in den 60er-Jahren. Seitdem ist die Recyclingindustrie stark gewachsen und die Nachfrage steigt weiter. Anbauer: „Es zahlt sich einfach aus, industrielle Reste aufzubereiten und wiederzuverwenden.“ In der Konstruktion, Fertigung und Servicierung steht ATM vor den gleichen digitalen Herausforderungen wie andere Firmen auch. Die Entwicklung optimiert u. a. die Serviceprozesse: „In Zukunft werden MitarbeiterInnen von einem digitalen Maintenance-Manager erfahren, wann die Maschine zu warten ist. So wird beispielsweise ein einzelnes Lager seine erhöhte Vibration wahrnehmen und melden, dass es in 17 Tage auszutauschen ist“, erklärt Andreas Anbauer. Schon jetzt lösen die MitarbeiterInnen auf unterschiedlichen Kontinenten Probleme gemeinsam virtuell. Die nötigen Kompetenzen, etwa die Prozessdatenerfassung, erwerben die Angestellten Schritt für Schritt.
Das Angebot der ständigen Weiterentwicklung, die vielseitige Tätigkeit im internationalen Kontext und die persönliche Note des 52-Köpfe-Betriebs kommen offensichtlich gut an. „Wir haben MitarbeiterInnen, die vor Jahrzehnten bei uns gelernt haben und in den nächsten drei bis vier Jahren hier in Pension gehen.“